On Zeme Zivitelka fair, Ceske Budejovice, CZ, Zetor has announced to introduce a new tractor model with 120-171hp. Zetor North America says it is the new Forterra , available from third quarter of 2024. What is clear is that it has a completely new cab, but we will follow what details will be publicized in the next week.
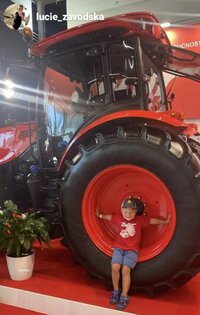
As can be seen, it has a steel sickle above the mudguard, like the Proxima.
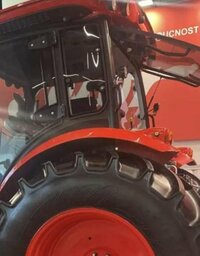
This is because the cabs have been placed higher on Crystal and Forterra to improve operator visibility, which left a bigger gap between tire and mudguard at the back, with the previous cab.
Possibly this allows for more room above the wheels to install the more ergonomic hydraulic control levers of the Proxima in the HSX too.
Other noticeable change is the doors are bigger, the B pillar of the cab is moved roughly 20cm back, and the door hinges are different.
Will this new Forterra have a Deutz TCD 4.1 up to 171hp ? Or will the Forterra be available in both 4 and 6 cylinder like Deutz-Fahr ? We will report as soon as more news comes out...
Because of the current price level of the Forterra, ergonomic or technical flaws are not permissible for Zetor, even at basic spec tractors they require to have their ergonomics (placement and logic of the controls, feel, noise, vibration, harshness) spic and span...
Spotted by Forum member twan hag
This message edited with new information 30-08 9:45pm
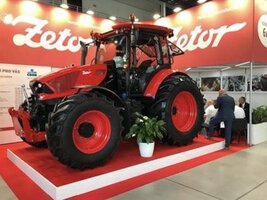
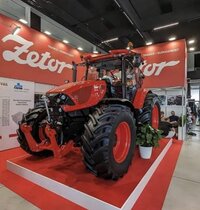
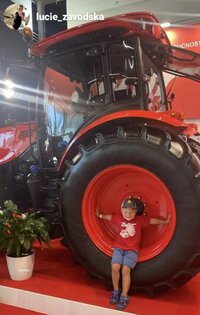
As can be seen, it has a steel sickle above the mudguard, like the Proxima.
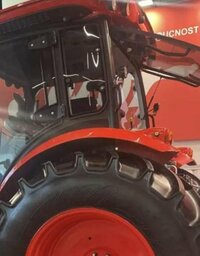
This is because the cabs have been placed higher on Crystal and Forterra to improve operator visibility, which left a bigger gap between tire and mudguard at the back, with the previous cab.
Possibly this allows for more room above the wheels to install the more ergonomic hydraulic control levers of the Proxima in the HSX too.
Other noticeable change is the doors are bigger, the B pillar of the cab is moved roughly 20cm back, and the door hinges are different.
Will this new Forterra have a Deutz TCD 4.1 up to 171hp ? Or will the Forterra be available in both 4 and 6 cylinder like Deutz-Fahr ? We will report as soon as more news comes out...
Because of the current price level of the Forterra, ergonomic or technical flaws are not permissible for Zetor, even at basic spec tractors they require to have their ergonomics (placement and logic of the controls, feel, noise, vibration, harshness) spic and span...
Spotted by Forum member twan hag
This message edited with new information 30-08 9:45pm
Last edited: